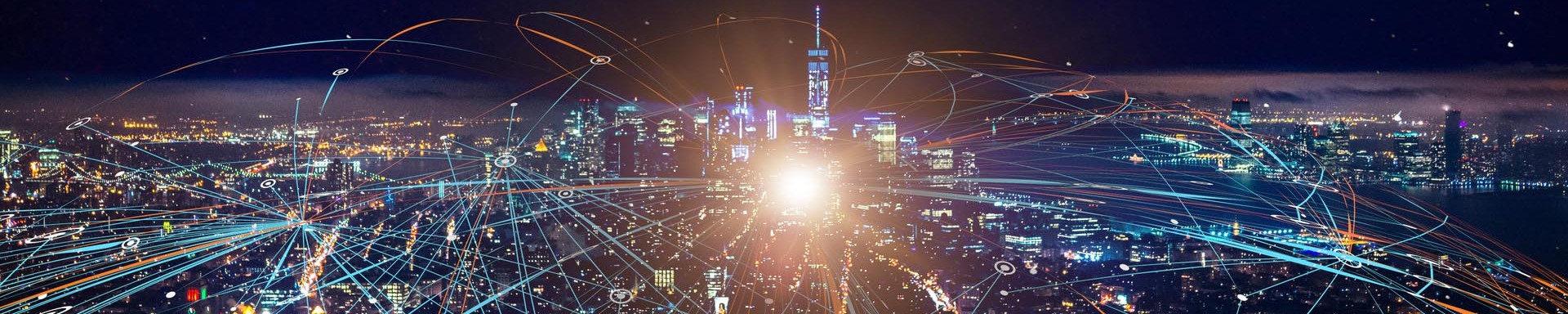
Production and application of BTTZ rigid mineral insulated fireproof cable
2023-03-02 09:00Production and application of BTTZ rigid mineral insulated fireproof cable
Abstract: the development history, production mode, precautions and installation points of BTTZ cable.
1.Introduction
BTTZ copper core copper sheathed magnesium oxide insulated heavy-duty fire-resistant cable is a high-performance fire-resistant cable made of copper conductor, inorganic insulating material (magnesium oxide powder) and seamless copper pipe or copper strip welded by longitudinal cladding. These three materials are processed by multiple drawing or rolling. This cable has the characteristics of high temperature resistance, fire protection, explosion-proof, non combustion (continuous long-time operation at 250 ℃, and short-time operation for 30min under the limit state of 1000 ℃), large current carrying capacity, small outer diameter, high mechanical strength, long service life, and generally does not need independent grounding conductor. It has a wide range of applications, and can be used at sea, on land, indoors and outdoors, above ground and underground; In particular, it is widely used in historical buildings, super high-rise buildings, hotels, shopping malls, hospitals, airports, TV stations, communication hub projects, ships, theatres, subways, civil air defense projects, crowded public places, and dangerous places prone to fire (such as natural gas plants, chemical plants, oil refineries, off shore oil platforms, etc.). It can also be used in places with high ambient temperature, such as power plants and steel plants. It has also been applied to special environments, such as anti electromagnetic interference, anti animal
bite, waterproof and nuclear power station.
2.Development history of BTTZ mineral insulated cable
The early inventor of mineral cable was Arnold Francois Borel, a Swiss engineer, who proposed at the end of the 19th century. He first proposed the idea of using magnesium oxide powder as an insulating material to achieve fire resistance and high temperature resistance, and obtained an invention patent. Since then, it has been widely produced and applied in developed countries such as Britain, France, Italy, the United States and Japan. In 1991, China promulgated the national standard gb13033 mineral insulated cables and terminals with rated voltage of 750V and below, but the formulation and revision of the corresponding design standards and specifications failed to keep up, resulting in the slow development of the use and promotion of mineral cables in China, lagging behind the developed countries. In 2007, the new national standard GB / t13033-2007 mineral insulated cables and terminals with rated voltage of 750V and below was issued. So far, mineral cables in China began to develop.
3.BTTZ cable production mode
There are mainly two ways to produce BTTZ series cables in China, one is magnesium oxide porcelain column assembly and multiple drawing annealing. The main process flow of this method is porcelain column pressing, porcelain column sintering, cable assembly, multiple drawing annealing, water immersion test, etc. This method was first adopted in China. Its main feature is that it fills the gap that our country cannot produce BTTZ cable, and has the advantages of stable performance and high drawing efficiency. Because it adopts seamless copper tube assembly, the wire body will not be cracked and other damages during the drawing process, and the pass rate of voltage withstand test is high. The disadvantage is that the processes are complex and cannot be formed at one time, and a large space is required to place various equipment, and a large number of manpower is also required. Due to the limitation of the length of seamless copper pipe and the extension coefficient of copper material, the cable produced by this method can not reach a long meter section. Moreover, at present, BTTZ cables need to use special connectors during construction and installation. Such special connectors are expensive, complicated and time-consuming. Many connectors are required for long-distance wiring, which adds a lot of extra costs to users. Another production method of BTTZ cable is a method commonly used in China at present. According to the main process, we temporarily named it as high-frequency annealing production line for copper strip longitudinal cladding argon arc welding continuous binding. This method can save space and human resources to the maximum extent. It is proved that only 3 people can produce qualified cables at one time, and the length of cables can be produced according to the requirements of customers, which greatly reduces the difficulty of construction and installation of customers and effectively reduces the number of special connectors.
4.Problems needing attention in BTTZ cable laying
(1) BTTZ cable is hard, so crossing shall be avoided as much as possible during laying.
Before laying, the "cable laying route map" shall be drawn according to the design drawings, and the number, specification, length, direction, position of intermediate joints and spacing of crossing with other pipes shall be carefully checked. The laying shall be carried out on the special cable paying off rack, and sufficient operation margin shall be reserved when handling intermediate joints and terminal heads.
(2) The cable circuit shall be numbered and marked . The number and phase sequence of each circuit shall be marked by hanging signboards or pasting permanent signs at the end and starting points of each circuit, at each intermediate joint, and at the hole through the wall, so as to avoid the error of circuit and phase sequence connection due to too many circuits and joints.
(3) Reduce eddy current loss
In practical application,BTTZ cables are mostly composed of single core cables, so it is easy to generate induction eddy current in cable fixing fittings. If the eddy flow is large, it will not only generate a large amount of eddy current loss but also accelerate the aging speed of the fixed fittings of the cable. Therefore, the eddy current shall be avoided or minimized in the actual construction process. The cables are usually bound with non-metallic fasteners on site, and reasonable cable phase sequence arrangement is adopted to minimize the generation of eddy current.
(4) Moisture proof cable
Before laying, carefully check the insulation value and whether the end and copper sheath are exposed and scratched. Sealing shall be carried out in time after discovery. Paraffin is generally prepared as temporary sealing material on site. During setting out, the sawn off part of the remaining part shall also be sealed immediately. Ensure that moisture in the air does not enter the insulation layer.
(5) Bending of cables
When laying the T-shaped bend, L-shaped bend, crossing wall hole, electric shaft, incoming and outgoing distribution cabinet box and other places with large bending degree and small space, pay attention to the balance of force during laying. When handling the bending, conduct cold bending according to the bending method and strength specified in the installation instructions, and do not bend manually.
(6) Protection after cable laying in the same bridge, the cables with different phase sequences in the same circuit shall be laid at the same time. After laying, the bridge cover plate shall be covered in time for protection to prevent the cables from being damaged and burned by tools, building materials or welding sparks during the construction of other disciplines, thus causing damage to the cable outer sheath.